IndiaSoft Technologies (P) Ltd.
DUA Building, 2nd Floor, Ghule Patil Road, Near Raheja Vista Premiere, Mohammedwadi, Pune – 411060.
Ph. : +91 9325111066, E-mail: rkirani@indiasoft.co.in, mail@indiasoft.co.in, www.indiasoft.co.in
Powerful & Intuitive Modeling, Simulation & Optimization Tools
Engineering Simulation Solutions

3D Manufacturing Plant Modeling & Advanced Robotics OLP Simulation Services:
Complete 3D Manufacturing Plant with PLC Interface/ Specific Manufacturing Processes / Custom Machines with Integrated Robotics, Throughput Reports, Advanced Robotics OLP & more.
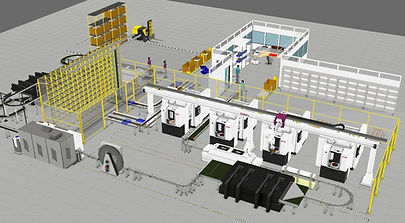

Our simulation services include:
Factory Planning
-
Building the digital twin
-
Spacial requirements
-
Workflow simulation
-
Resource planning
-
Identification of KPI through charts and dashboards
-
Production analysis with statistics and reports
-
Identification of bottle-necks
Packaging Systems
-
Packing machines such as box erectors, sealers, wrapping machines, pallet dispensers etc.
-
Transport with variety of resources like Conveyors, lifts, AGVs, Forklifts, humans etc.
-
Packaging with robots, gantries, humans or SPMs
-
Variety of picking logics based on part type, vision system inputs
-
Variety of palletizing logics based on imported CSV files, manual definition etc.
-
Complete analysis of the plant with various types of statistics and reports
Storage and Warehousing
-
Manual warehousing with operators such as godowns
-
Automatic storage and retrieval systems with storing in various zones
-
Simulate buffering possibilities
-
Analyse the inventory levels, plant through-put,
-
Track picking and retrieving efficiencies
Robotics
-
Simulate any robot and analyse cycle times, collisions, reachability
-
Applications such as BIW, Arc Welding, Spot Welding, machine tending, 3P(pick-place-palletize)
-
Robot Offline Programming (OLP)
We help customers to Visualize their ideas, analyse the real-world implications of the ideas and take the step forward to implement in the reality.
Whether it is optimizing existing processes or conceptualizing new ones, we help our customers to achieve the results by building a digital twin or a virtual replica.
Through simulation, we help customers to analyze key indicators such as Profitable product mix, Down-time implications and Alternate solutions to existing processes.
Our Services include:
Factory Planning
-
Layout Preparation
-
Identification of ideal process flow and simulation
-
Planning of resources such as Workers, AMR, Robots, etc.
-
Best possible navigation routes
-
Effective utilization of resources
-
Analysis of bottlenecks, throughput, cycle-time studies, the feasibility of the plant
-
Complete report with results and recommendations
Robot Simulation & Offline Programming
-
Offline cell preparation
-
Identification of best robots for the job
-
Simulation, Cycle time studies, reachability, collision analysis
-
Support for all major robot brands
-
Cell calibration and commissioning of offline programs on the real system
-
Complete report with results and recommendations
​
How our customers benefit:
Boost your efficiency by up to 30%
Increase efficiency in your manufacturing operations with our virtual commissioning tools, enabling precise control over process performance through simulation and validation of designs with PLCs and robot controllers.
Save costs by up to 15%
Design many what-if scenarios in hours instead of days, have better insights into your projects, minimize your investment and save additional costs from your projects.
3000+ ready-made CAD components
Use our extensive library of 3D models with more than 1,600 robots, 70+ brands, and a wide range of conveyors, machines, resources, robot tools, factory facilities and more.
Reduce robot programming time by up to 80%
Program your robots more quickly and efficiently than with traditional manual programming methods. Test and optimize your programs before downloading them to the physical robots.
Maximize robot utilization by up to 95%
Optimize your robots’ utilization with fast and easy offline programming for tasks such as welding, material processing, or spray painting and eliminate robot downtime.
Enhance safety
Reduce the risks of accidents and injuries by programming heavy-duty industrial robots through offline programming software. Program from anywhere without any risk of robot collisions or physical accidents.
​​​
Client List of Projects Executed:
-
Anzo Controls Pvt. Ltd.
-
Atlas Copco India
-
Bajaj Auto Limited
-
Hitech Robotic Systems
-
Gudel India Pvt. Ltd.
-
KUKA Systems
-
Mitsubishi Electric India Pvt. Ltd.
-
TATA Consultancy Services Ltd.
-
Thyssenkrupp Automotive Body Solutions Private Limited
-
Vasundhara Automation & Engg. Services Pvt Ltd.
-
Wheels India Ltd.
-
Wipro Pari
-
Yaskawa